ElectroSlag Remelting Furnaces
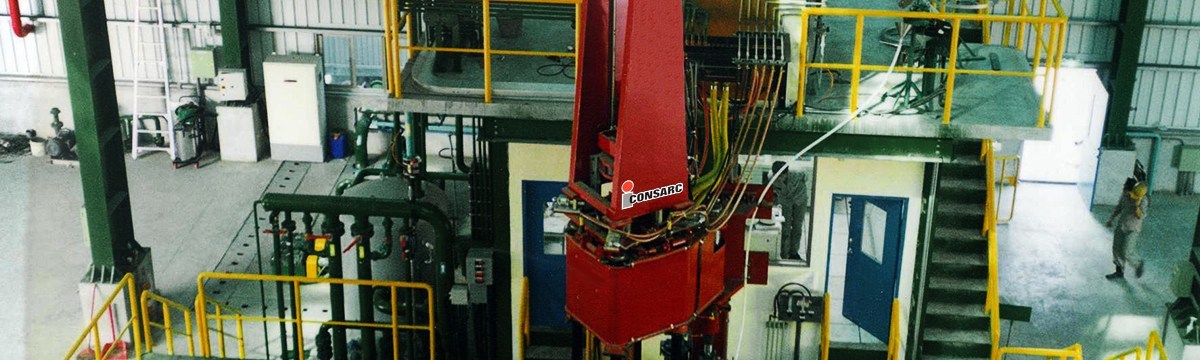
In the 1960s Consarc’s engineers conceived a new approach to electroslag remelting, quite different from others in use at the time. The resulting improvements in the efficiency and performance of the process established Consarc as the leading manufacturer of ESR systems worldwide.
What Consarc’s engineers did was to combine the use of a “high fill ratio” electrode (an electrode whose diameter approaches that of the crucible) with an AC line frequency furnace design in which the main power conductors were arranged coaxially around the melt zone. The high fill ratio electrode provides significant benefits, including reduced power consumption, increased ingot quality, and improved ingot surfaces.
The coaxial conductor system allowed the use of smaller, more efficient power supplies and decreased undesirable magnetic stirring of the melt. Moreover, it virtually eliminated the stray field eddy current heating of surounding steelwork which had characterized all prior ESR furnace designs and allowed magnetic interaction between adjacent melts.
The principles of this coaxial design are incorporated in all ESR furnaces produced by Consarc.
Features
• Fully coaxial
• Precision electrode drive
• Fully automated melt control
• X-Y electrode centering
• Inert gas melting capable
• Dry air melting capable
• Slab ingot capable
• Dry slag starting capable
• Liquid slag starting available
• Purpose designed AC power supplies
Tech Specs
Dry or Liquid Slag Start Capable:
Most ESR furnaces today are started “cold” with dry prefused slag. Consarc can also provide a slag melting furnace with the ESR system that gives “hot” (liquid) slag start capability. This is most useful in situations where humidity and moisture are concerns, as well as in locations where sourcing of prefused slag is problematic.
Purpose Designed AC Power Supplies:
Consarc is the only ESR furnace supplier that designs and builds our own power supplies. These units are specifically designed to meet the demanding requirements of the ESR melting application. This provides Consarc ESR customers with a single source responsibility for the complete ESR and power transmission system.
Inert Gas Melting System:
Today many Oxygen and Nitrogen sensitive alloys are melted under an inert gas atmosphere. The major benefits of the Inert Gas Melting System are:
• Helps improve control Oxygen and Nitrogen levels in the final ingot compared to melting in air or dry air
• The system is fully enclosed, preventing the possibility of contamination from the melt shop during melting
• Different slags can be used because the oxidation of the slag is no longer a concern
• Minimal to no deoxidant is required; deoxidant can be a principal source of inclusions in ESR ingots.
• Alloys requiring higher nitrogen levels can be remelted in an inert gas atmosphere that includes a higher percentage of nitrogen, reducing the outgassing of that element from the alloy