Vacuum Cap Furnaces
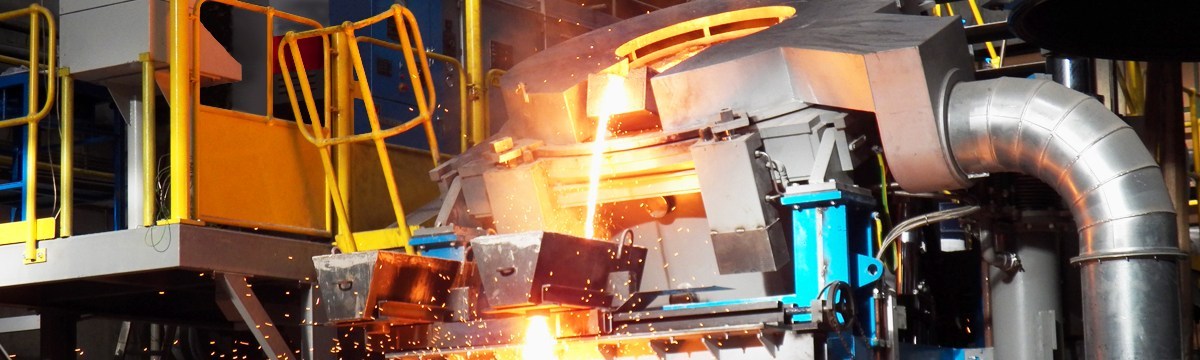
The VCAP furnace is designed for Induction Melting a solid charge in an air atmosphere (or vacuum), with final degassing stage under vacuum. The final pouring of the metal is performed in air or under protective atmosphere of inert gas. Configuration is based on the Inductotherm range of steel shell induction furnaces which are fully adapted by Consarc for vacuum treatment of liquid metal.
Features
Some typical processes that can be performed in the VCAP range include:
- Air melting from solid charge (option for vacuum melting)
- Controlled atmosphere melting from solid charge
- Alloy homogenization and chemistry adjustment
- Vacuum degassing (hydrogen and nitrogen removal)
- Reduction of low vapor pressure tramp elements (e.g. Pb, Cd, Bi, Zn)
- Deoxidation using combination of vacuum and C-O reaction
- Decarburization – Intensified C-O reaction at low pressure enabling decarburization for lower carbon levels.
- Argon purging of metal with porous plug
Some of the more important customer product advantages from VCAP operation are:
- Generally significant improvement of mechanical properties, such as yield strength, ductility, impact strength, fatigue and stress rupture elevated temperature properties.
- Improvement of technological characteristics, such as hot workability, weldability and machinability.
- Better micro-cleanliness due to strong carbon deoxidation and smaller residual inclusions.
- Significantly reduce scatter in product properties and characteristics, less rejections.
Tech Specs
The VCAP furnaces are available to suit a wide variety of application in sizes ranging from 50 kg to 20 tonnes.
Accessories
- Vacuum melting
- Inert gas pouring
- Porous plug inert gas (argon) purging
- Furnace back-tilting
- Automated vacuum lid handling
- Fume extraction ring
- Optical pyrometer
- Vacuum isolated sampling and fines charging
- Scrap and raw material charging
- Hydraulic lining push-out
- High voltage supply transformer
- Dry Screw pumping systems
- SCADA supervisory control systems
- Outer Loop Cooling System (Open or Closed)